Contenuti trattati
Il massetto è quello strato costruttivo orizzontale a copertura del sottofondo, che serve a livellare la superficie finale della pavimentazione, e a fare da supporto al rivestimento finale.
Perché un massetto sia realizzato a regola d’arte è necessario che risulti perfettamente piano e raccordi in modo complanare l’intera superficie della casa, prevedendo lo spessore finale del rivestimento (lastre, piastrelle, parquet), al fine che anch’esso non abbia poi salti di quota – pure in caso di compresenza di finiture differenti – e si riescano a movimentare senza problemi le ante di porte e porte-finestre.
Cosa serve per realizzare un massetto?
Le componenti di un massetto sono generalmente tre, miscelate in opportune proporzioni: legante (solitamente il cemento), inerte (come la sabbia) e acqua. Il loro dosaggio varia in base alla destinazione d’utilizzo e alla resa che si desidera abbia lo strato finito. Spesso si aggiungono poi additivi ad hoc per potenziarne le prestazioni: è il caso ad esempio delle palline di polistirolo per il massetto alleggerito, delle fibre sintetiche per il massetto fibrato che limita le fessure in fase di asciugatura, delle fibre metalliche per il massetto rinforzato e ad elevata conducibilità termica.
Rete per massetto collaborante
In alcuni casi particolari, quando sia necessario rendere il massetto più collaborante con il resto della struttura architettonica o si debba rinforzarlo è possibile annegare nel suo spessore una rete metallica elettrosaldata, che ne aumenti la rigidità e nel contempo ripartisca il carico.
Tipologie di massetto
Massetto sabbia e cemento
Il massetto tradizionale è composto in genere da cemento, sabbia e acqua, miscelati e amalgamati direttamente in cantiere con le piccole betoniere mobili su ruote.
Massetto premiscelato
Oggi sono molto diffusi anche i prodotti premiscelati, venduti in sacchi, a cui aggiungere solo acqua: si tratta di mix ad hoc per situazioni architettoniche e funzionali diversificate, con additivi appositi che ne potenziano le diverse qualità (ad esempio polistirolo, fibre sintetiche o metalliche).
In base alle speciali componenti e di conseguenza alle caratteristiche specifiche, dunque, i massetti possono rientrare in altrettante categorie, tra cui:
- massetto alleggerito, contenente palline di materiali sintetici o naturali (polistirolo o argilla espansa) che ne riducono il peso specifico
- massetto fibro-rinforzato, addittivato con fibre sintetiche o metalliche per aumentarne la coesione e la resistenza
- massetto ad elevata conducibilità termica, ideale per riscaldamenti a pannelli radianti
- massetto autolivellante, particolarmente fluido, che si distribuisce uniformemente.
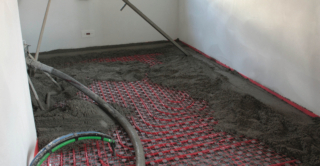
Massetto ad elevata conducibilità termica di Fassa Bortolo
Quanti centimetri deve essere spesso un massetto?
Lo spessore del massetto varia in base alla tipologia costruttiva dell’edificio, all’altezza del sottofondo e al tipo di rivestimento finale desiderato: in linea di massima va da 1 cm (con i prodotti premiscelati autolivellanti) a 6/8 cm circa. Se si ha necessità di uno strato più spesso, per evitare peso eccessivo sul solaio sottostante ed eventuali fessurazioni al momento della maturazione (come viene tecnicamente chiamata l’asciugatura) conviene optare per un massetto alleggerito.
La quota finale desiderata, data dalla somma di sottofondo, massetto, rivestimento, va calibrata prendendo come riferimento la soglia d’ingresso preesistente della casa e “battendo” (ovvero riportando con lo speciale spago impolverato blu o con un metro di legno o, più tecnologicamente, con uno strumento laser) sulle pareti circostanti 1 metro di altezza da essa. Sarà questa la misura finita a cui fare riferimento per l’opera terminata, in ogni ambiente dell’unità immobiliare.
Massetto posato a regola d’arte
La norma UNI EN 13813:2004 “Massetti e materiali per massetti – Materiali per massetti – Proprietà e requisiti” specifica le qualità necessarie dei componenti di un massetto, ma oltre a ciò è necessario valutare i fattori di una esecuzione a regola d’arte, ovvero perfetta per l’utilizzo e le prestazioni richieste.
Innanzi tutto è importante la stesura della miscela – affinché non si creino disomogeneità nella mescola e/o grumi – del prodotto scelto (tradizionale o premiscelato), successivamente il rispetto delle quote predefinite e infine la lisciatura, indispensabile per avere una superficie più regolare possibile ai fini della corretta posa della pavimentazione superiore. Le ultime due fasi operative vengono attuate mediante l’uso di una staggia, una barra metallica di lunghezza adeguata all’ambiente con cui livellare e regolarizzare il materiale levandone quello in eccesso.
Spessore del massetto in base al rivestimento
Ovviamente è indispensabile valutare gli spessori dei rivestimenti finali, perché possono avere dimensioni diverse: resine e pavimentazioni di linoleum sono particolarmente sottili (fino al massimo 5/7 mm), ma le piastrelle di ceramica o di gres si aggirano su 1 cm, così come il parquet (che però può arrivare anche a 2 cm), mentre le lastre di pietra raggiungono valori maggiori (2/3 cm). A ciò si deve poi aggiungere il minimo ingombro della posa in opera, se a colla o flottante (direttamente sul massetto, previa eventuale interposizione di un apposito materassino). Alcuni prodotti di finitura, come ad esempio le lastre di pietra e il cotto di un certo spessore, possono essere anche posati a malta, ovvero sfruttando la morbidezza del massetto stesso come letto di posa, prima che sia asciugato.
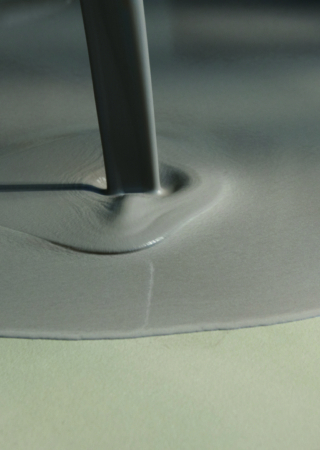
Posa autolivellante di Kerakoll (www.kerakoll.com)
Posa del massetto a macchina
Quando le superfici da realizzare sono particolarmente estese, si può ricorrere alla posa del massetto a macchina, mediante pompaggio della miscela da mezzo su ruote a piano strada oppure con apparecchiature automatiche più piccole, che lavorano e distribuiscono il mix in cantiere. Rispetto alla posa tradizionale, in questo modo i tempi si riducono, anche se il costo può aumentare. L’automazione tra l’altro permette di ottenere miscelature controllate – nei casi più evoluti anche con software – con le giuste dosi dei diversi ingredienti.
Differenza tra sottofondo e massetto
Un solaio è fatto da due elementi: massetto e sottofondo. Il massetto è applicato sopra il sottofondo, che è uno strato di calcestruzzo (alleggerito o meno) poggiante direttamente sul solaio strutturale dell’edificio, atto a ripartire i carichi soprastanti e a regolarizzare eventuali dislivelli.
Spesso nel sottofondo sono annegati gli impianti tecnici, soprattutto quelli condominiali (come elettrico e idraulico, oltre che di riscaldamento), ma non i pannelli radianti, che vengono posati su questo strato e ricoperti con il massetto.
Cosa mettere tra sottofondo e massetto
Tra sottofondo e massetto può essere posata una barriera al vapore, vale a dire uno strato impermeabile all’acqua – di polietilene, pvc o alluminio -, che impedisca la risalita di umidità dalla struttura portante alla pavimentazione, se questa risulti particolarmente sensibile (come può essere il legno).
In caso di massetto solidale con il sottofondo o quando in una ristrutturazione si intenda rimuovere solo il rivestimento superficiale per sostituirlo, si può pensare di inserire tale barriera tra il massetto e la pavimentazione, per proteggere comunque quest’ultima dall’umidità. A volte la barriera può essere anche fonoisolante al calpestio.
Tempo di asciugatura di un massetto
Il massetto tradizionale ha un tempo di maturazione (vale a dire di asciugatura) molto lungo – che in particolari situazioni ambientali può arrivare anche oltre 20 giorni – e ciò può risultare problematico quando si abbia necessità di chiudere in fretta un cantiere o di posare un rivestimento sensibile alla presenza di acqua, come ad esempio il parquet o la resina. In tal caso si può optare per prodotti specifici, in grado di garantire una asciugatura più veloce, che in tal caso può ridursi fino a qualche giorno per spessori di massetto minimi. Il valore di riferimento in ogni caso è il grado di umidità del massetto, misurabile con un igrometro apposito e tassativamente inferiore al 2% in tutto lo strato.
Per posare i pavimenti ceramici (inclusi cotto, gres, pietra, marmo e qualsiasi altro materiale non patisca l’umidità) si può invece attendere meno tempo, vale a dire almeno 10 giorni dalla realizzazione del massetto.
Quando rifare un massetto?
Le problematiche più frequenti che segnalano una posa in opera non a regola d’arte di un massetto sono la sua friabilità priva di compattezza, l’irregolarità superficiale, la presenza di fessurazioni, fino ad arrivare, nei casi più gravi, al distacco dal sottofondo.
Tutto ciò dipende sia da una lavorazione inadeguata sia da condizioni ambientali inidonee: ad esempio il mancato rispetto delle istruzioni del produttore, in caso di prodotto premiscelato, oppure una elevata temperatura esterna, che porta il cemento a seccarsi troppo in fretta o ancora la mancata attenzione di posa in punti critici della stanza, come possono essere i pressi di elementi strutturali verticali o gli angoli.
Difetti molto evidenti, che precludano di conseguenza una posa perfetta della pavimentazione, richiedono la demolizione e il rifacimento del massetto. Se tuttavia i problemi sono esclusivamente superficiali – come ad esempio una mancata complanarità della superficie, con avallamenti o gobbe, si può ricorrere a una successiva rasatura di livellamento, previa stesura di primer aggrappante.
Shock termico del massetto per riscaldamento a pavimento
Quando si è in presenza di un sottofondo con riscaldamento a pannelli radianti per evitare problematiche future al massetto è possibile ricorrere al cosiddetto shock termico: ad avvenuta maturazione dello strato cementizio (secondo quanto prescritto dal produttore in caso di premiscelato o a decorrere di almeno 20 giorni per un mix tradizionale) si accende il riscaldamento e gradualmente lo si porta alla temperatura di esercizio per alcuni giorni, facendo poi calare altrettanto gradualmente la temperatura. In tal modo si sottopone il massetto a uno stress che ne renda immediatamente evidenti i vizi di realizzazione (se si formano le crepe) e nel contempo lo si porta al grado stabilizzazione finale, con evaporazione della eventuale umidità residua, prima della posa del rivestimento.
Massetto per esterno su terra
Il massetto non è uno strato strutturale, ma va a completare un sottofondo portante. Tuttavia, per realizzazioni in esterno, quando si abbia a disposizione un terreno “nudo”, si può considerare la realizzazione di uno strato cementizio, a patto però di rispettare alcune regole. Innanzi tutto è fondamentale la compattazione della terra, mediante appositi macchinari; successivamente si può posare del materiale inerte (ghiaia) di granulometria differente, a seconda della portanza che si vuole dare al risultato finale. Da ultimo si realizza il massetto, rinforzato però dalla presenza di una rete metallica elettrosaldata, che renda la superficie coesa e resistente.
Quanto costa realizzare un massetto?
Il prezzo al metro quadrato di un massetto varia molto in base alla tipologia di prodotto utilizzato e alla metodologia di posa. In linea di massima si passa da circa una decina di euro per un massetto tradizionale di sabbia e cemento, steso e livellato a mano, per arrivare anche al doppio o al triplo in caso di soluzioni più performanti.
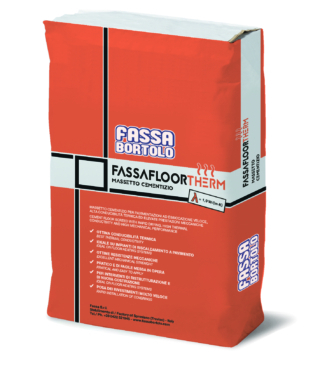
Massetto FASSAFLOOR Therm di Fassa Bortolo (www.fassabortolo.it)
FASSAFLOOR Therm di Fassa Bortolo è un massetto cementizio ad alta conducibilità termica, studiato per ottimizzare le prestazioni dei sistemi di riscaldamento e raffrescamento a pavimento senza bisogno di ulteriori additivi. A consistenza semi-umida e a presa ed essiccazione veloci, risulta ottimale per la posa di ogni tipo di rivestimento (legno, linoleum, PVC, moquette, LVT, gomma, materiali lapidei, piastrelle in ceramica, resina).
L’autolivellante per massetto Planogel Rheo di Kerakoll, certificato a base di materie prime a basso impatto ambientale non irritanti, combina reologia e viscosità variabili: la prima consiste nella possibilità di modulare l’acqua d’impasto del prodotto per regolarne la fluidità, in base agli spessori da realizzare e alle abitudini del posatore. La viscosità variabile è invece la proprietà dell’impasto gel di modificare la sua consistenza in base alle sollecitazioni a cui è sottoposto. Così il fondo di posa del rivestimento risulta planare, resistente e stabile.
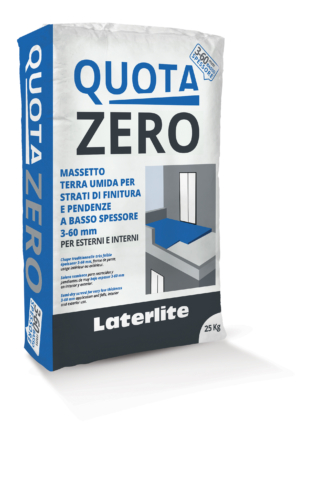
Massetto a basso spesore QuotaZero di Laterlite (www.leca.it)
QuotaZero di Laterlite è un massetto terra umida per strati di finitura e pendenze a basso spessore (da 3 a 60 mm), adatto sia a esterni sia a interni. La sua specifica formulazione consente la realizzazione di ampie superfici senza necessità di reti e/o giunti di dilatazione. La semplicità di modifica di pendenze o livellamenti in strati sottili su pavimenti esistenti consente di regolarizzare o ripristinare la planarità e dare un nuovo aspetto agli ambienti, senza dover necessariamente intraprendere opere di ristrutturazione invasive.
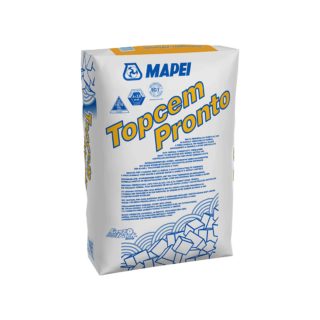
Massetto Topcem Pronto di Mapei (www.mapei.com)
La malta pronta all’uso Topcem Pronto di Mapei, ad alta conducibilità termica quindi ideale per massetti riscaldanti, è a presa normale con ritiro controllato, per un veloce asciugamento (4 giorni).